Cone crusher repairs. Cracks developed in the mainframe of these 2 crushers – repairs on different machines carried out over the last 2 years.
Crusher 1 [Feb. 2010]
Crack No. 1 originally had crack depth variations from14 to 30mm – second test 16-31mm. Crack length approx. 220mm. Cast Steel Parent material showed some variation in hardness typical in larger castings requiring use of carbide drills in some areas.
Crack No. 2 [close to gear] originally had crack depth variations from 9 to 20mm – 2nd test 10 -20mm and had 2 adjacent cracks which were also repaired. Crack length approximately 250mm including adjacent / splinter cracks.
Background pictures of crusher and main frame.
Cracks 1, 2 prior to repairs
Crack 1. Total length of crack 220mm. 9 sets of No 4 metalock keys [2 metalock keys x1 deep at ends, 3 sets at 2 deep with the balance 4 deep – some 24 locks in total ] were positioned across fracture and spaced approximately 20mm apart. Keys of 5 and 7 length lugs were used. Locks are parallel in form and were installed /stacked as required to depths prescribed by Ultrasonic depth testing
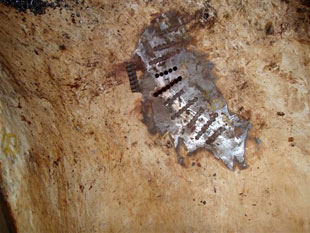 |
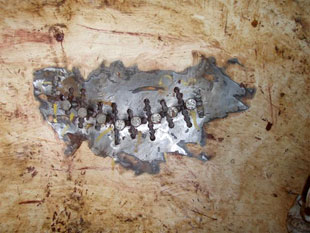 |
1. Lock aperture, and jig drilled are prior
to lock installed |
2. Locks installed, screws fitted |
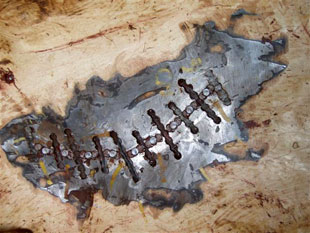 |
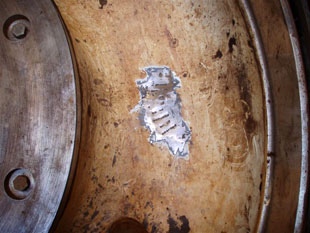 |
3. Screws cut off prior to peening / grinding |
4. Finished repairs |
Crack 2. Total length of crack 250mm. 7 sets of No 4 locks [2 metalock keys x 1 deep at ends, 1 set at 2 deep with the balance 3 deep – some 16 locks in total] were positioned across fracture and spaced approximately 20mm apart. Whilst normally Keys of 5 and 7 length lugs are used, the operator may fit longer length ie 9 lug Keys, in order to further distribute the strength over cracks running parallel or splintering when in close proximity as was the case here [1 off 8 lug length key used at end of fracture furthest away from gear, 3 sets of 9 lug locks - 2nd closest to gear side]. Locks installed to depths prescribed by Ultrasonic testing.
Note: Metalock key material used was a special proprietary product especially made for Metalock International Association. Designated MN555, the lock material is a Nickel Alloy:
Crusher 2 [Oct. 2011]
Variations to crack depth and crack length from what was found in initial ultrasonic test were considerable and required eventual removal of pinion gear to access fracture which had carried through that area. Dye Penentrant Testing used to verify crack length.
Crack No. 1 had crack depth variations from 8mm to 25mm and Crack length was approx. 450mm including splinter crack. Parent material showed some variation in hardness typical in larger castings. Carbide drills required in a few spots.
Crack No. 2 RHS of gear well facing front of crusher had crack depth variations from 9 to 20mm Crack length approximately 45mm
Background pictures of crusher and main frame Cracks 1, 2 prior to repairs.
Crack 1. Total length of crack 450mm. 16 sets of No 4 metalock keys [6 metalock keys x1 deep at ends, 4 sets at 2 deep with the balance 3 deep – some 36 locks in total ] were positioned across fracture and spaced approximately 20-25mm apart. Keys of 5 and 7 length lugs were used [1 set 9 lug long]. Locks are parallel in form and were installed /stacked to depth as required. 8mm studs as fitted along length of fracture between metalock keys.
Crack 2. Total length of crack 45 mm. 2 sets of No 4 locks [2 metalock keys x 1 deep were positioned at ends of fracture - Locks installed to depths. 8mm studs as fitted along length of fracture between metalock keys.
Screws installed / cut off prior to peening / grinding then metalock key aperture is jig drilled and pneumatic ripped with sized blades prior to lock installation.
Finished repairs with pinion oil return area radius ground and polished as required.